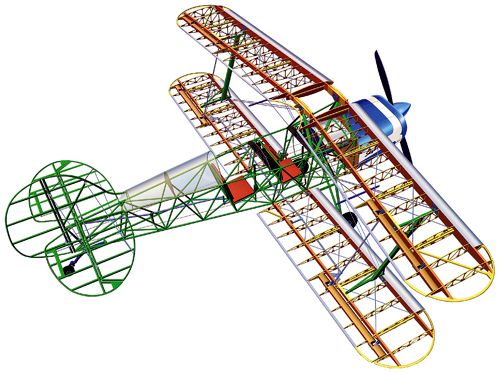 |
Vediamo qui come sono fatti i velivoli dal punto di
vista strutturale.
L'obiettivo è imparare un po' di nomenclatura (centine, correnti,
longheroni ...) e capire quali sono i problemi e come li si
risolvono.
La "struttura" è ciò che tiene insieme le parti del velivolo che
abbiamo visto fin'ora, le ali che generano portanza, la fusoliera,
destinata a contenere il "carico pagante" e a collegare le ali ai
piani di coda, gli organi di comando aerodinamici (ali e piani di
coda), l'apparato propulsivo egli organi d'atterraggio.
Intanto cominciamo a distinguere tre tipi fondamentali di struttura,
la struttura a telaio, quella a guscio e quella a semiguscio.
In aeronautica sono utilizzate tutte e tre, a volte insieme.
La struttura a traliccio è una struttura composta da tralicci in legno
o metallo che vengono poi rivestiti, in genere da tela.
Nella struttura a traliccio tutte le sollecitazioni vengono assorbite
dal telaio metallico, lasciando al rivestimento la sola funzione
di generare il carico aerodinamico.
Nella struttura a guscio, invece, il rivestimento è parte integrante
della struttura e contribuisce ad assorbire le sollecitazioni.
La struttura a semiguscio è una struttura a guscio, dove però sia
possibile individuare dei componenti particolari (i longheroni) che
garantiscono la resistenza a flessione, mentre al rivestimento è
lasciata la sola reazione agli sforzi di torsione. |
I primi velivoli erano costruiti con strutture "a
traliccio", in genere in legno, rivestite in tela.
Tale soluzione, però, si rivelava inadatta alle alte velocità cui
già si era arrivati alla fine della I Guerra Mondiale.
Furono perciò realizzati velivoli rivestiti in metallo, e a questo
punto sembrò stupido non considerare anche il rivestimento in
alluminio quale componente strutturale, visto che c'era comunque e
pesava, e l'allumino presentava caratteristiche meccaniche
decisamente superiori alla tela e anche allo stesso legno che ancora
costituiva l'ossatura interna, subito anch'essa costruita in
alluminio..
Da allora sostanzialmente non vi furono grandi evoluzioni, ed oggi
le strutture aeronautiche sono generalmente a guscio per la
fusoliera e a semiguscio per le ali e gli impennaggi in genere.
Le evoluzioni notevoli sono state invece realizzate nella tipologia
dei materiali, dove le leghe di alluminio hanno lasciato spazio ai
materiali compositi, sia metallici che plastici.
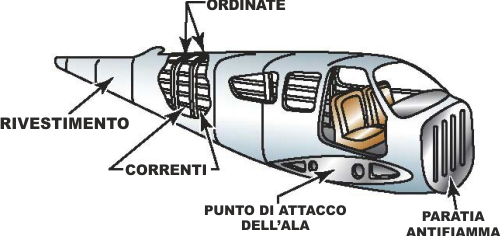 |
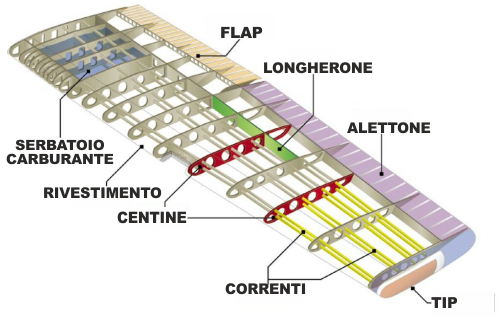 |
Le
sollecitazioni strutturali |
Per semplificarci la vita si analizza una struttura in
relazione a sollecitazioni che vengono semplificate il più
possibile, in modo da poter poi calcolare e realizzare la
struttura stessa nel modo più conveniente, facendo in modo
che siano componenti specifici a reggere a sollecitazioni
specifiche.
Le sollecitazioni "base" più semplici con cui abbiamo a che
fare sono la trazione-compressione (assiali) e il taglio
(diagonale).
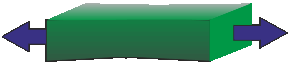 |
Trazione - La struttura è soggetta ad un carico
che tenda ad "allungarla" e basta.
Una struttura semplicissima che sicuramente subisce
solo questo tipo di sollecitazione è il cavo, che
essendo flessibile può sopportare solo trazione. |
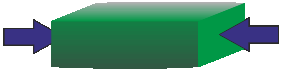 |
Compressione - Come per la trazione la struttura
è soggetta ad un carico semplice assiale, ma questa
volta nel che tende a "schiacciarla".
Sono strutture semplici destinate a questo tipo di
carico, ad esempio, le colonne in pietra, formate da
elementi semplicemente sovrapposti, che si
sposterebbero se la compressione non fosse
perfettamente assiale.
In modo più complesso, ma sostanzialmente identico
sono in genere sollecitate a compressione tutti gli
elementi di un muro o in genere di un'opera in
pietra. Esempio mirabile di come si possa
trasformare una sollecitazione complessa come quella
relativa ad un ponte in una semplice compressione
per i singoli componenti che lo costituiscono è
l'arco romano in mattoni.
Un'altra struttura semplice, soggetta a carichi
distribuiti e vari che però si comporta come se
fosse soggetta solo a compressione è l'albero di una
barca a vela, dove la flessione (che vediamo dopo)
viene trasformata in compressione (sul "palo") e
trazione (sul sartiame).
In teoria un elemento metallico sollecitato
a compressione avrebbe una resistenza
enorme, in realtà quando abbiamo a che fare
con elemento "snelli" il problema è che in
pratica non è possibile garantire che il
carico sia applicato perfettamente, cioè che
la sollecitazione permanga esclusivamente
assiale.
Basta infatti una minima eccentricità perché
la struttura si deformi "arcuandosi" e il
carico si trasformi da assiale a composto,
sollecitando l'elemento a flessione e
facendolo collassare.. |
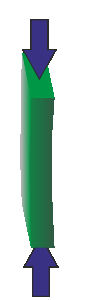 |
|
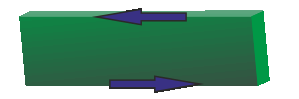 |
Taglio - E' una sollecitazione "diagonale", ove
le fibre del materiale tendano a "scorrere2 le une
sulle altre.
La sollecitazione di taglio in effetti "non esiste",
ma si può considerare come una sollecitazione di
trazione/compressione inclinata diagonalmente
rispetto all'asse principale della trave.
Vedremo meglio questo concetto quando tratteremo i
tralicci, dove appunto l'anima di una trave
(tipicamente l'elemento sottoposto a taglio) è
sostituita da un elemento soggetto a sola trazione o
a compressione. |
Componendo le sollecitazioni che
abbiamo visto prima si descrivono altri due "tipi",
e cioè la "flessione" e l "torsione", che quindi
vengono ad essere sollecitazioni "composte". |
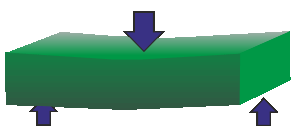 |
Flessione - Si ha flessione quando un trave
tende, appunto, a flettersi, cioè ad incurvarsi.
Il caso tipico di flessione è la trave appoggiata o
incastrata caricata con un peso. |
La flessione va analizzata con attenzione, in quanto
è di fatto il tipo di sollecitazione più gravoso su
cui vengono dimensionate le strutture.
Un'ala, ad esempio, si può vedere come una trave su
cui sia distribuito un carico (la portanza) e ne sia
collegato uno di senso opposto alla radice (il peso
della fusoliera e del carico in essa contenuto). |
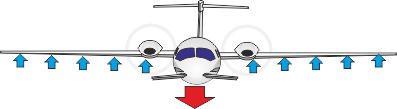 |
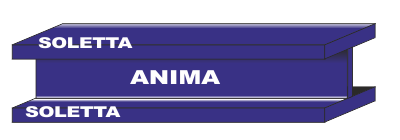 |
La classica trave destinata a sopportare tale tipo
di sollecitazione è il "doppio T", una trave
composta da due "solette" e un'"anima" che le
collega.
Quando la trave è sollecitata a flessione le due
solette lavorano a trazione e a compressione, mentre
sull'anima si sviluppa una sollecitazione diagonale,
di taglio. |
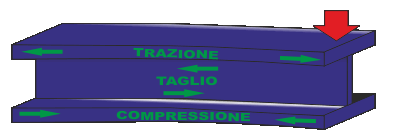 |
|
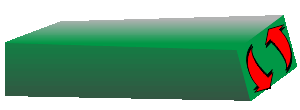 |
Torsione - Un elemento è sottoposto a torsione
quando le sue sezioni sono sollecitate a ruotare
attorno ad un asse.
La torsione è una sollecitazione composta, si può
vedere come uno sforzo di taglio distribuito sulla
superficie delle'elemento. |
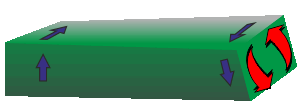 |
|
|
|
La
struttura a traliccio |
Il "traliccio" è una struttura "semplice", dove tutti
gli elementi sono soggetti solo a sforzi assiali di trazione
o di compressione. |
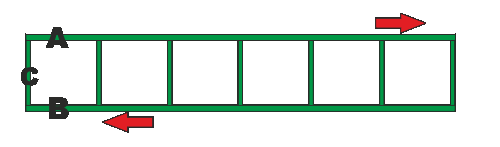 |
I caso . struttura LABILE - Il traliccio è
composto solo da elementi ortogonali. Tale sistema
non è capace di sopportare alcuno sforzo di taglio
(e quindi nemmeno la torsione, come vedremo più
avanti).
Nel traliccio tutti gli elementi sono "snelli",
quindi capaci solo di sopportare sollecitazioni
assiali pure (trazione o compressione).
Se applico una situazione di "taglio" sulla
struttura questa collassa senza che alcun componente
possa in qualche modo reagire. |
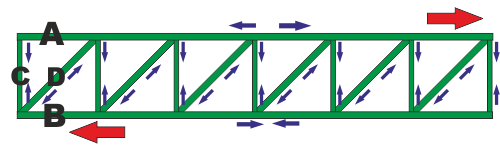 |
Se invece inserisco degli elementi diagonali
questi impediscono la deformazione del reticolo.
In questo caso tutti i componenti reagiscono alla
sollecitazione e il sistema non collassa. |
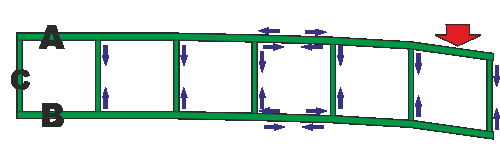 |
Vediamo come reagirebbe "in teoria", il sistema
visto all'inizio ad una sollecitazione di flessione.
I due elementi A e B reagiscono alla flessione come
la trave vista prima, stirandosi su una faccia e
comprimendosi su un'altra, gli elementi C
trasferiscono solo la compressione data dal carico e
fanno lavorare le due travi in parallelo. |
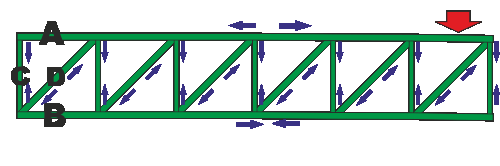 |
Se invece inserisco l'elemento diagonale D
questo si carica a trazione e fa lavorare il sistema
come un'unica grande trave dove i componenti C e D
fanno la parte dell'anima e i componenti A e B
diventano le due solette, caricate una a
compressione e l'altra a trazione.
Anche senza far calcoli particolari, è subito
intuitivo che un sistema del genere è molto più
efficace rispetto a quello visto nell'esempio
precedente.
Da questa visualizzazione si comprende meglio anche
cosa è realmente lo sforzo di taglio, e cioè di
fatto uno sforzo di trazione/compressione inclinato
rispetto all'asse della trave.
Notate che se il carico fosse in senso opposto il
diagonale D manterrebbe comunque la stabilità del
sistema, ma sarebbe caricato a compressione.
|
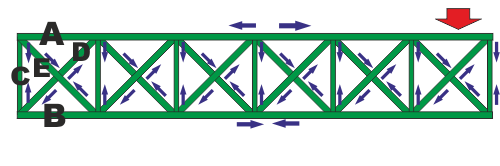 |
Supponiamo infatti di avere una trave reticolare
con due tiranti diagonali ortogonali tra loro, lo
sforzo sarebbe distribuito come nello schema a lato.
In questo caso il diagonale D è caricato a
trazione come nel caso precedente, mentre il
diagonale aggiunto E è caricato a compressione.
Se il carico fosse nel senso opposto sarebbe il
diagonale D a comprimersi mentre E sarebbe stirato.
La scelta di utilizzare un diagonale o due dipende
dal fatto che gli elementi caricati a trazione
reggono meglio che a compressione e, di fatto, in
una trave del genere i due diagonali D ed E si
potrebbero sostituire con dei tiranti in cavo,
sottili e leggeri.
Questa trave è assolutamente equivalente a quella "a
doppio T" con le due solette e un'anima "piena". |
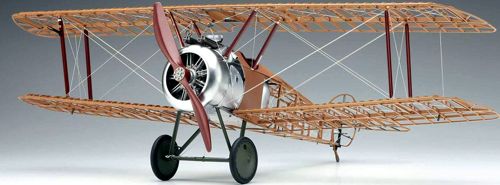 |
I primi velivoli erano spesso in formula "biplana",
cioè con due ali collegate tra loro da sottili
tiranti.
I tiranti ovviamente possono essere caricati solo a
trazione e di conseguenza ce ne devono due più o
meno ortogonali, in modo da mantenere il sistema
stabile in qualsiasi condizione di carico.
In questo modo le due ali collaborano tra loro come
le due solette di una trave a doppio T. |
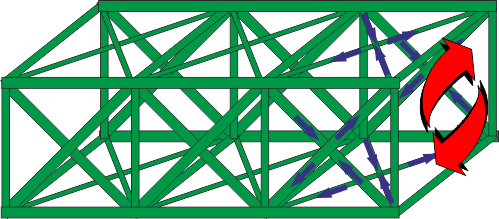 |
La torsione viene contrastata dagli elementi
diagonali, che lavorano a due a due a trazione e
compressione.
Perché la struttura possa reggere a torsione occorre
perciò che sia "chiusa".
Questo concetto lo vedremo meglio con un facile
esempio quando parleremo delle strutture a
semiguscio.
Gli elementi assiali risultano scarichi.
Le strutture a traliccio risultano le più semplici
da realizzare, non necessitando di particolari
sagomature dei componenti.
Sono leggere e possono essere realizzate con vari
materiali. |
|
|
La
struttura a semiguscio |
|
|
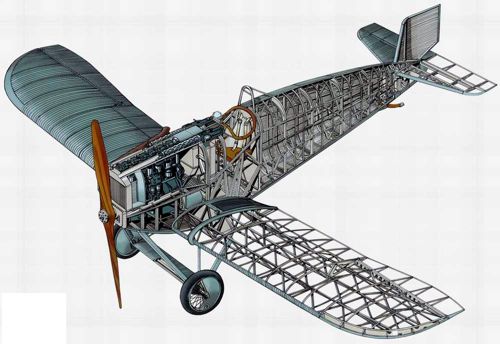 |
Già alla fine della I Guerra Mondiale, gli aerei erano capaci di
sviluppare velocità nell'ordine dei 200 km/h e fu evidente che
l'architettura in legno e tela non era adatta per i velivoli sempre
più veloci che la tecnologia a questo punto permetteva di costruire.
Anche se non utilizzato in combattimento, già nel 1915 lo Junkers
D.1 era un velivolo costruito integralmente in metallo.
Quando il rivestimento divenne di metallo, fu naturale pensare di
utilizzarlo come parte integrante della struttura, destinandogli
sostanzialmente il compito di contrastare la torsione.
Le strutture così realizzate sono composte da una o più travi
principali, con lo scopo di sopportare la flessione, detti
"longheroni", da centine destinate a mantenere la forma
aerodinamica, sostanzialmente conformate come "travi" trasversali al
longherone, da "correnti" di irrigidimento che contribuiscono alla
resistenza a flessione e fungono da supporto al rivestimento, e
finalmente dal rivestimento, che irrigidisce la struttura, sino ad
ora labile rispetto alla torsione. |
 |
Per capire il concetto pensiamo ad una semplice
esperienza.
Prendiamo 4 matite sufficientemente spesse da poter stare in
piedi, disponiamole a formare un quadrato e appoggiamoci
sulla punta un peso, ad esempio un libro.
Le matite, dopo qualche tentativo, potranno anche reggere il
libro (se il libro viene appoggiato delicatamente e lasciato
in pace, le quattro matite risultano caricate a
compressione), ma se avviene una minima perturbazione il
nostro sistema crolla.
Se adesso prendiamo le stesse matite, ma le uniamo con una
striscia di carta in modo da circondarle tutte (stendiamo la
striscia di carta, ci appoggiamo sopra le matite e ce le
incolliamo, poi la pieghiamo in modo che si richiuda su se
stessa e quindi incolliamo i due bordi terminali), e poi ci
appoggiamo sopra lo stesso libro, la struttura stavolta
regge bene sia il libro, sia eventuali perturbazioni. |
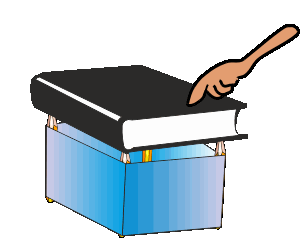 |
|
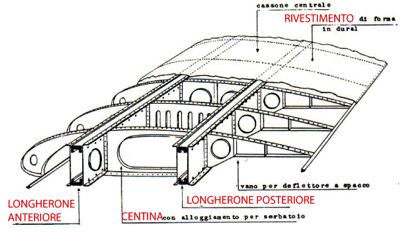 |
Il longherone -
Il longherone è l'elemento destinato a reggere a flessione.
Di fatto è una trave in cui è possibile isolare due solette
ed un'anima esattamente come nelle travi a doppio T per
edilizia viste in precedenza. |
Come abbiamo visto per queste travi i carichi maggiori
sono sopportati dalle due solette, mentre l'anima serve solo
a trasmettere gli sforzi di taglio, collegando tra loro le
solette che, ricordo, lavorano una a compressione e una a
trazione.
Nelle travi aeronautiche, ove contenere il peso è
fondamentale, l'anima è sempre molto sottile e spesso
forata, sia per alleggerirla, sia per permettere il
passaggio dei componenti necessari al funzionamento dei vari
impianti (cavi elettrici e/o tubazioni idrauliche). |
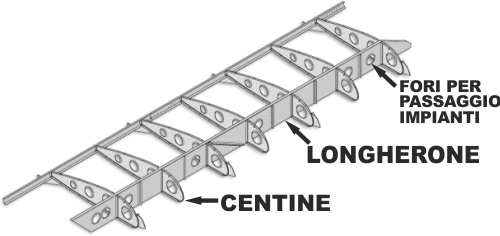 |
|
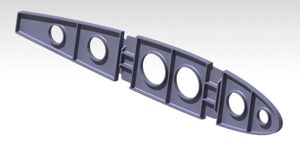 |
Le centine - Le centine
sono, di fatto, travi complete, quindi anch'esse possono
essere viste come un insieme di due solette e un'anima.
Sono destinate per lo più a mantenere la forma della sezione
alare, ma servono anche quali punti di forza per
l'applicazione di carichi puntuali quali le gondole con i
motori, eventuali serbatoi
supplementari, armi, e, a volte, il carrello di atterraggio.
Sono per lo più realizzate in lega d'alluminio stampata e
interrotte ove necessario per far passare il longherone
I componenti corrispondenti alle centine dell'ala, nella
fusoliera si chiamano "ordinate". |
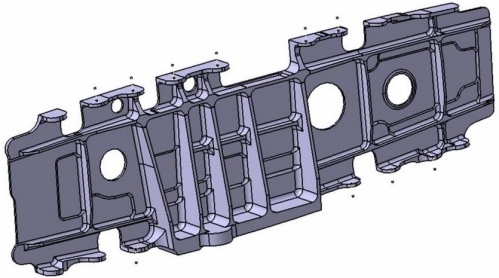 |
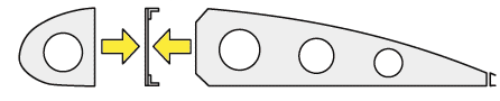 |
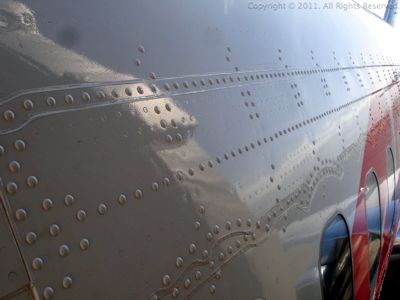 |
Il rivestimento - Nella
struttura a semiguscio il rivestimento metallico concorre
alla resistenza strutturale, in particolare garantendo la
rigidità a torsione.
Dal punto di vista strettamente strutturale in realtà il
rivestimento potrebbe essere sottilissimo. Spesso viene
dimensionato sulla possibilità di essere collegato ai
correnti e alle centine mediante chiodatura o sulla capacità
di reggere ad urti accidentali piuttosto che non per la vera
e propria funzione di tenuta a torsione.
Sui velivoli di linea, inoltre, il rivestimento ha il
compito di mantenere la pressurizzazione interna.
I velivoli pressurizzati normalmente hanno sezione di
fusoliera perfettamente circolare, che è la forma più
conveniente per un contenitore di gas compresso. |
|
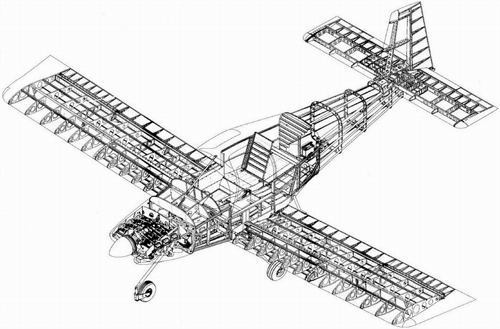 |
|
L'ala |
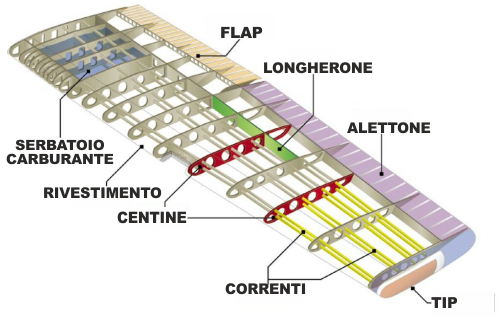 |
La struttura dell'ala comporta normalmente
uno o due longheroni (raramente di più) continui, cui sono
collegate trasversalmente le centine.
Le centine conferiscono la forma aerodinamica e fungono da
supporto per tutti i carichi esterni (dalle gondole dei
motori ai pod per agganciare carichi vari, ai fissaggi degli
organi attuatori dei flap e degli alettoni).
Sulle centine sono poi collegati i correnti che
contribuiscono, come si è visto, alla resistenza a flessione
e servono quale supporto per il fissaggio del rivestimento.
Se la struttura è bilongherone, spesso è individuabile uno "scatolato"
confinato tra i due longheroni. che costituisce la reale
struttura resistente dell'ala. E' infatti "chiuso" tra il
rivestimento esterno e le anime dei longheroni.
A questa cassa sono poi collegati a sbalzo gli elementi
terminali delle centine.
Normalmente all'interno dell'ala sono alloggiati i serbatoi.
Questi devono essere suddivisi da settori longitudinali e
trasversali in modo da limitare lo "sciacquio" del
carburante che potrebbe se no spostare in modo inopportuno
il baricentro.
Le centine sono per lo più forate per permettere il
passaggio dei cavi elettrici e dei tubi dei sistemi
idraulici. |
|
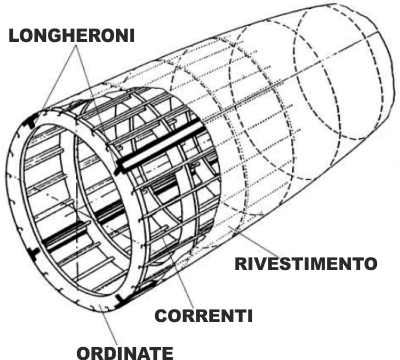 |
La fusoliera è formata da elementi detti "ordinate" che
di fatto sostituiscono le centine dell'ala, cui sono
collegati i correnti longitudinali.
Date le grandi dimensioni e quindi la grande distanza tra la
parte superiore e quella inferiore, spesso la struttura è
sufficientemente robusta senza la necessità di individuare
dei veri e propri longheroni.
Quando l'aereo è pressurizzato la fusoliera è di forma
cilindrica a sezione circolare, comportandosi a tutti gli
effetti come una "bombola" di gas compresso.
A volte anche la tensione dovuta alla pressione interna può
essere considerata nella valutazione della robustezza
strutturale.
Se questo avviene poco o nulla per i normali velivoli, è, ad
esempio, una voce fondamentale nella valutazione della
rigidità dei due grossi serbatoi di idrogeno che servono lo
Space Shuttle; questi elementi, in fatti, da vuoti non
sarebbero in grado di regger alcuna sollecitazione, neanche
quella dovuta al peso proprio della struttura, e
collasserebbero.
Nelle fusoliere pressurizzate ha grande importanza il
posizionamento degli elementi terminali e il design delle
aperture (portelloni e finestrini).
In seguito ad incidenti disastrosi che videro coinvolti sin
da subito i velivoli pressurizzati (ad esempio i De
Havilland Comet) il rivestimento viene oggi applicato in
modo da definire delle zone a "rottura limitata", in modo
che un'eventuale rottura localizzata del rivestimento non
possa degenerare in una
decompressione esplosiva. |
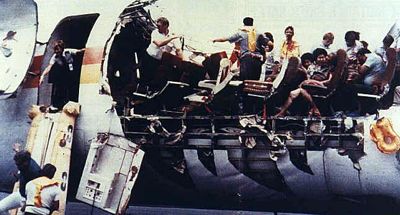 |
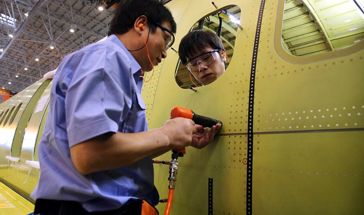 |
Dinamica
della frattura |
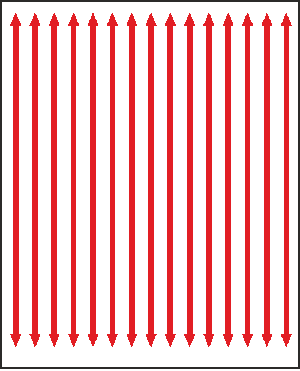 |
Facciamo una breve parentesi per vedere
quali sono i meccanismi di propagazione di una frattura.
Supponiamo di avere un elemento sottoposto ad uno stato di
sollecitazione semplice, ad esempio a trazione.
Possiamo facilmente supporre che lo sforzo si distribuisca
in modo simmetrico su tutto il materiale. Per semplicità
immaginiamo di visualizzare lo "sforzo" con delle linee
continue, nelle condizioni iniziali queste saranno tutte
egualmente distribuite e continue.
Se però sul nostro pezzo si genera un inizio di frattura,
una piccola incisione, le linee di tensione in prossimità
della frattura sono interrotte e quindi lo sforzo che prima
passava per la zona incisa deve essere in qualche modo
ridistribuito.
Se lo sforzo si ridistribuisse uniformemente sulla porzione
di materiale integra, sostanzialmente non avremmo grossi
danni, ma il fatto è che, ragionevolmente, la porzione
dell'elemento lontana dalla frattura non si "accorge" della
singolarità .. di fatto su tutto il resto del nostro
componente le linee di tensione restano quelle che erano.
Solo sulla parte immediatamente vicina alla frattura avremo
una ridistribuzione delle linee di tensione. La linea che
sarebbe stata interrotta dalla frattura "devia" e va a
scaricarsi sulle superfico vicino all'apice di questa.
In questo modo in quella zona, localmente, la tensione
aumenta notevolmente.
Può quindi succedere che anche se il carico, ridistribuito
sulla sezione ancora buona del nostro componente, non lo
farebbe collassare, così concentrato localmente è invece in
grado di produrre un ulteriore incremento della frattura.
All'aumentare delle dimensioni della singolarità, con lo
stesso principio, le linee di tensione si addensano sempre
in prossimità dell'apice della frattura, moltiplicando ad
ogni passaggio l'intensità dello sforzo sopportato
localmente.
Questa evoluzione della frattura può avvenire molto
lentamente, e spesso è favorita da fenomeni di ossidazione
che localmente intaccano il materiale.
Quando lo sforzo diventa abbastanza grande la frattura si
espande in modo istantaneo (frattura esplosiva) e si ha il
cedimento improvviso dell'elemento. |
Per comprendere l'effetto provate a prendere un foglio
di carta e tirarlo. Il foglio mostrerà una certa resistenza.
Ora sullo stesso foglio praticate un piccolo strappo e poi
provate a stirarlo come in precedenza.
Noterete che con il foglio si strapperà con uno sforzo
decisamente inferiore a quello che poteva sostenere in
precedenza. |
|
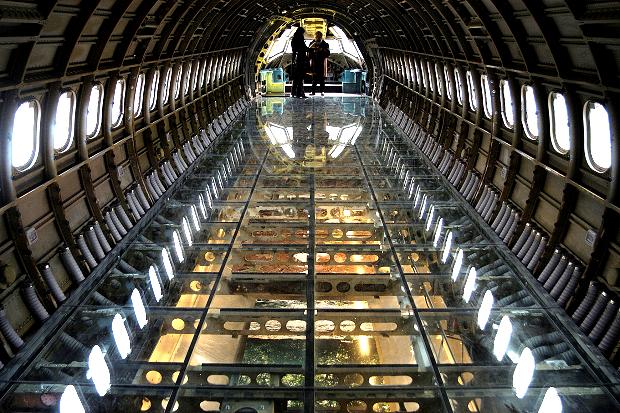 |
All'interno della fusoliera devono essere realizzate le
solette che servono al posizionamento del carico. Queste
sono veri e propri solai in carpenteria metallica e vengono
dimensionati in funzione del tipo di carico che si intende
stivare, che va dai pochi kg del "passeggero", dove se
vogliamo il carico dimensionante può essere il peso
concentrato di un essere umano distribuito sulla superficie
di un piccolo tacco (non a spillo, che a bordo dovrebbero
essere vietati), ai carri armati che devono poter manovrare
all'interno di velivoli come il C-5 Galaxy. |
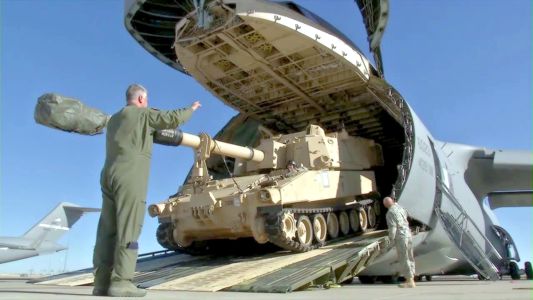 |
|
|
|
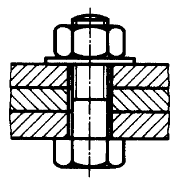 |
La bullonatura - In questo tipo di giunzioni gli
elementi (i bulloni) sono sollecitati a trazione, e l'azione
di fissaggio dei componenti che si vogliono collegare è
svolta dall'attrito che si viene ad esercitare tra i
componenti stessi, "compressi" tra loro dalla tensione
esercitata dal bullone.
Per poter distribuire adeguatamente tale tensione, è
necessario un componente essenziale che è la "rondella". In
assenza di tale componente la tensione esercitata dal
bullone potrebbe danneggiare gli elementi che si vogliono
giuntare.
La tensione esercitata dal bullone, infatti, invece di
distribuirsi sulla grande superficie della rondella, si
concentrerebbe sulla piccola superficie della testa
esagonale (spigolosa) del bullone stesso, arrivando ad
incidere, ad esempio, le lamiere sottili. |
Le giunzioni bullonate hanno il vantaggio di essere molto
resistenti e di poter essere agevolmente rimosse. In
compenso sono pesanti e costose.
In aeronautica quando si giuntano insieme due componenti
mediante bullonatura, occorre garantire l'efficienza del
collegamento e cioè che il dado, accidentalmente, non si
sviti.
Per questo si utilizzano sistemi di bloccaggio (spinotti o
rondelle "Glover") e si applicano dei segni di riferimento
sugli elementi, in modo che ad un'ispezione visiva sia
subito evidente l'allentamento della giunzione.
Le giunzioni bullonate non devono mai essere lubrificate, e
la tensione di serraggio corretta è di solito garantita
dall'utilizzo di apposite chiavi dinamometriche, che
permettono una coppia di serraggio massima predefinita. |
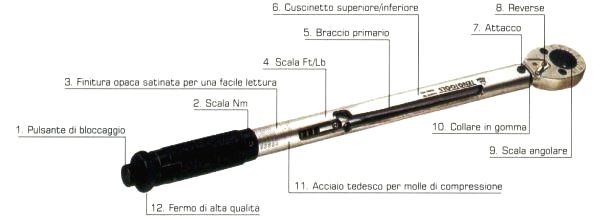 |
|
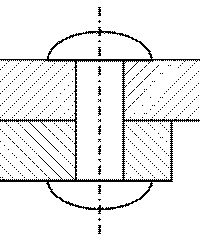 |
Chiodatura - Il chiodo, in carpenteria metallica, è un
elemento "duttile" che viene inserito in un foro e quindi
fissato mediante ribattitura.
Il chiodo, non potendo garantire nel tempo la tensione,
lavora semplicemente a taglio. Gli elementi giuntati non
possono muoversi in quanto il chiodo crea un'interferenza.
Il vantaggio della chiodatura è l'economicità e la
leggerezza. Il collegamento risulta permanente e
relativamente debole (a parità di carichi in gioco occorrono
molti più chiodi che non bulloni per realizzare giunzioni
simili.
In aeronautica i chiodi vengono utilizzati sistematicamente
per fissare il rivestimento esterno.
I chiodi possono essere normali o a testa fresata. Questi
ultimi, non sporgendo dalla superficie del rivestimento,
generano meno interferenza aerodinamica e quindi sono
preferibili sotto il profilo prestazionale, in compenso sono
più difficili da posizionare, in quanto gli elementi devono
essere prima adeguatamente preparati per poterli accogliere. |
|
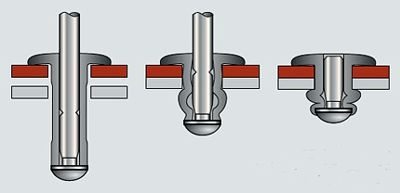 |
Rivettatura - Il rivetto è un particolare chiodo che
viene posizionato senza bisogno di dover accedere ad
entrambi i lati per poter essere ribattuto.
Il rivetto è un chiodo cavo di materiale duttile all'interno
del quale è passato un "chiodo" di materiale più duro. Una
volta fissato il rivetto in posizione il "chiodo"
all'interno viene tirato, in modo che la sua testa deformi
il rivetto che in questo modo non potrà più sfilarsi. Il
chiodo viene tirato sino a quando non si spezza (il chiodo è
realizzato in modo da spezzarsi per una tensione
predefinita).
Rispetto alla chiodatura è meno efficace. Resta sempre il
problema della testa a perdere del "chiodo" che "cade"
all'interno (nella zona inaccessibile)o che resta nel
rivetto (e in quel caso può concorrere alla resistenza a
taglio di questo). |
|
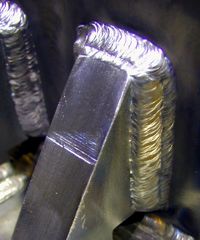 |
Saldatura - La saldatura è un procedimento che comporta
il riscaldamento di parte dei due elementi da giuntare sino
ad ottenerne la fusione locale. Successivamente,
raffreddandosi, i due elementi risultano collegati in teoria
come se fossero stati realizzati direttamente fusi insieme.
Teoricamente la saldatura ottiene una connessione
perfettamente continua dei due pezzi che si vogliono
giuntare, ma, in pratica, presenta alcune controindicazioni.
- Il surriscaldamento locale fino alla temperatura di
fusione annulla i trattamenti termici subiti dal
materiale in precedenza. Se questo è accettabile per
molti materiali ferrosi (semplici acciai al carbonio, ad
esempio) diventa poco attuabile su leghe particolari ed
in generale sulle leghe d'alluminio, che quindi
risultano saldabili con difficoltà.
- Se la saldatura eseguita con dispositivi automatici
risulta controllata e praticamente esente da
imperfezioni, molte volte la saldatura è eseguita
manualmente da un operatore. In questo caso l'efficacia
della giunzione è funzione della perizia dell'esecutore.
|
|
Le leghe
metalliche |
Sin dall'inizio della storia, l'uomo ha imparato ad utilizzare i
metalli, non tanto in quanto materiali puri, ma in combinazione tra
loro o con altri elementi.
Dapprima fu il bronzo, una lega (si definisce lega un composto
metallico ove i componenti non sono legati chimicamente tra loro,
come ad esempio ossigeno e idrogeno a formare un qualcosa di
completamente differente quale è l'acqua, ma semplicemente
"mischiati", in un materiale che conserva parzialmente le
caratteristiche dei componenti) di rame e stagno, più rigido del
rame e del poco utile stagno, capace di essere utilizzato per armi e
armature-
Poi, a migliorare le caratteristiche del ferro, venne l'acciaio
(inizialmente una lega di ferro e carbonio, che gli antichi romani
per primi seppero utilizzare accoppiata al trattamento termico più
semplice, la "tempera", che permetteva ai lori gladi di essere
enormemente più duri e resistenti delle rozze spade in ferro degli
avversari).
In aeronautica oltre agli acciai speciali (oltre al carbonio oggi si
utilizza un'infinità di altri elementi che conferiscono ai materiali
caratteristiche particolari di volta in volta adeguandoli alle
necessità di impiego) si utilizzano soprattutto le leghe di
alluminio, che rispetto alle leghe ferrose sono più leggere. |
|
|
I materiali
compositi |
Si definisce un materiale "composito" un materiale ove siano
identificabili delle "fibre" (carbonio, vetro, metalli vari) e una
"matrice" che serve a tenerle insieme in genere di materiale
plastico, ma oggi anche metallico o ceramico.
Nei materiali compositi la resistenza meccanica è ottenuta grazie
alle fibre, mentre la matrice serve a fornire la protezione dagli
agenti esterni.
La possibilità di posizionare le fibre in direzioni particolari
conferisce a questi materiali comportamenti diversi in funzione
della direzione della sollecitazione.
Un materiale composito semplice e naturale è, ad esempio, il legno.
Nel legno sono facilmente identificabili le fibre, e chiunque abbia
mai provato a tagliare con un'accetta dei blocchi di legno avrà
notato come questo sia duro e resistente se si tenta di intagliarlo
trasversalmente alle fibre, mentre si apre facilmente se lo si
colpisce parallelamente a queste. |
|
Aeroelasticità -
il flutter |
L'aeroelasticità è la scienza che studia il
comportamento di strutture flessibili (quali ad esempio le
ali o i ponti sospesi) sollecitate da una forza
aerodinamica.
Queste strutture si deformano a causa della forza
aerodinamica e la loro deformazione fa variare la forza
stessa.
Ad esempio, un'ala produce portanza, questa forza la carica
e se l'ala è abbastanza snella, si flette.
Flettendosi può (deve) variare l'incidenza relativa delle
varie sezioni, con la necessità che una flessione verso
l'alto (dovuta ad un aumento della portanza) generi una
rotazione della sezione dell'ala verso il basso (diminuisce
l'incidenza dei profili alari man mano che ci allontaniamo
dalla radice), in modo da diminuire il Cl e di conseguenza
la portanza (ad un aumento della portanza la struttura
reagisce in modo da "scaricarsi", se così non fosse la
portanza aumenterebbe ulteriormente sino a produrre il
sovraccarico dell'ala e il collasso). |
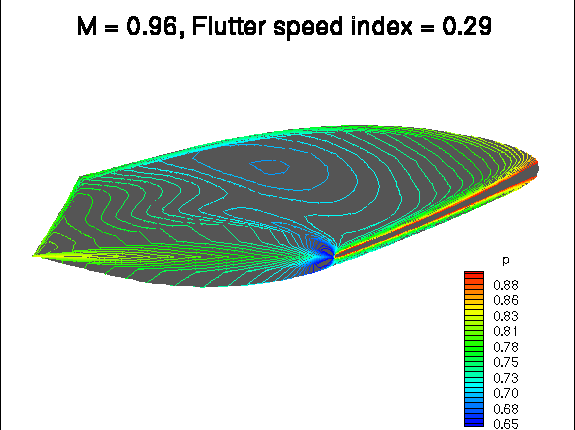 |
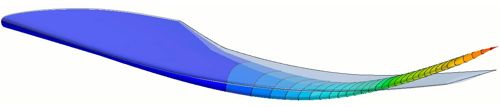 |
Il flutter è un fenomeno dannoso che si genera quando
questa risposta innesca oscillazioni di ampiezza crescente,
anche qui portando al collasso della struttura |
|
|
|
|